- HACCPの基準を満たす虫モニタリングの正しい手順
- 監査で「評価される」記録の付け方と、そのポイント
- 効果を最大化するトラップの設置場所と、やりがちな失敗例
- 自社対応か業者依頼かの判断基準と、信頼できる業者の見極め方
「虫の発生を防ぐモニタリング体制を整備したい」
「HACCP(ハサップ)の義務化に対応しないと…」
「監査が目前に迫っているが、今の対策で十分だろうか」
食品工場の品質管理や衛生管理を担当されている皆様は、このようなお悩みをお持ちではないでしょうか。
この記事では、私たちが数々の食品工場の現場で培ってきた経験とデータに基づき、HACCPに対応し、監査をクリアするための「食品工場における虫モニタリング」の具体的な方法を、分かりやすく徹底的に解説します。
私たち株式会社トータルクリーンは、業歴50年以上、累計施工実績12万件以上を誇る害虫・害獣駆除の専門会社です。その知見から、テレビ朝日「グッド!モーニング」といったメディアで専門家として解説させていただいた実績もございます。
この記事は私たちトータルクリーンが現場で対応してきた事例をもとに解説をしており、トータルクリーンで食品工場の防虫対策の責任者をしている角野がどのような視点でチェックしているかも説明しておりますので、この記事を読んでいただければ食品工場における虫モニタリングに関する基本的な取り組みやポイントを理解いただけると思います。
ぜひ、最後までご覧ください。
Table of Contents
そもそも食品工場の「虫モニタリング」とは?
食品工場における虫モニタリングとは、工場内外に潜む害虫の「種類」「数」「場所」を定期的に監視・記録し、そのデータを基にリスクを評価・管理する一連の科学的な活動のことです。
これは、単に「虫を捕まえる」という対策ではありません。
IPM(総合的有害生物管理)の考え方に基づき、問題の早期発見と原因究明、そして対策の効果測定を行うための重要な仕組みなのです。
※IPMとは、Integrated Pest Managementの略で、IPM(総合的有害生物管理)とは、化学薬剤だけに頼るのではなく、状況に応じて様々な防除技術を最適に組み合わせることで、有害生物を管理する手法です。このアプローチは、人の健康へのリスクと環境への負荷を最小限に抑えつつ、予め設定した管理基準まで有害生物を効果的に制御し、そのレベルを維持し続けることを目的としています。
参考サイト:「IPMという手法を駆使して」公益社団法人日本ペストコントロール協会
参考サイト:「IPMをご存知ですか?」東京都健康安全研究センター
効果的なモニタリングを行うことで、偶発的な害虫の発生に後手で対応するのではなく、データに基づいた計画的かつ予防的な衛生管理体制の構築が可能になるため、食品工場の防虫対策として非常に大切な取り組みです。
虫のモニタリングが重要な理由
モニタリングの重要性を理解していても、日々の業務に追われる中で「なぜここまで手間をかける必要があるのか」と感じることもあるかもしれません。
しかし、虫のモニタリングは、単なるコストではなく、企業の未来を守るための「投資」の位置づけといえます。ここでは、その3つの重要な理由を解説します。
理由1:HACCP制度化で必須となった法的要求事項
2021年6月から、原則としてすべての食品等事業者にHACCPに沿った衛生管理が完全義務化されました。
HACCPの考え方では、問題が発生してから対応するのではなく、あらかじめ危害要因(ハザード)を分析し、予防するための管理計画を立てて実行することが求められます。
HACCPとは、食品の製造工程における危害要因(ハザード)を分析し、重要管理点(CCP)を定めることで製品の安全性を確保する衛生管理手法です。
参考サイト:「HACCP(ハサップ)」厚生労働省
害虫の存在は、食中毒菌の媒介や異物混入につながる重大な危害要因です。
そのため、その状況を継続的に監視・記録する「モニタリング」は、HACCPプランが有効に機能していることを検証するための必須項目と位置づけられています。
理由2:製品汚染とブランド失墜を防ぐための防衛策
万が一、製品への虫の混入が発生した場合、その被害は計り知れません。製品回収にかかる直接的な費用はもちろんのこと、SNSなどを通じて瞬時に情報が拡散され、長年かけて築き上げた企業のブランドイメージや信頼は一瞬で失墜してしまいます。
食品工場における防虫対策としてのモニタリングは、こうした壊滅的な事態を未然に防ぐための最も効果的な防衛策です。
理由3:問題の早期発見と対策の最適化(コスト削減)
「虫が出たら殺虫剤を撒く」という場当たり的な対策は、根本的な解決にならないばかりか、不要な薬剤コストがかさむ原因にもなります。モニタリングによって「いつ、どこで、どんな虫が」発生しているかをデータで把握できれば、問題の根本原因(例えば、特定の搬入口からの侵入や、排水溝での発生など)を特定し、的を絞った効果的な対策が可能になります。
【実践マニュアル】虫モニタリング5つのステップ
ここからは、HACCPの考え方に基づいた、具体的なモニタリングの実践マニュアルを5つのステップで解説します。
この手順に沿って進めれば、誰でも体系的で効果的なモニタリングを始めることができます。多くの人が見落としがちなプロの視点も交えて解説しますので、ぜひ参考にしてください。
ステップ1:計画策定(Plan)- 監査官も納得するモニタリング計画とは
食品工場における虫のモニタリングは、行き当たりばったりで始めるものではありません。まず初めに、「何を、どこまで、どのように管理するのか」を明確にした計画を立てることが、成功の9割を決めると言っても過言ではありません。
1-1. 対象エリアと重要管理点(CCP)の特定
工場内の全てのエリアを同じレベルで監視するのは非効率です。まずは、原材料の受入から製造、包装、出荷までの各工程を洗い出し、特に衛生管理が重要なエリアを特定します。
具体的には、以下のような場所がモニタリングの重要管理点となります。
- 原材料の搬入口、製品の搬出口
- 原材料・資材の保管庫
- 製造ラインの周辺
- 廃棄物の保管場所
- 排水溝や水回り
1-2. 対象とする害虫の種類を決める
次に、自社の工場で特に問題となりうる害虫を定めます。これは、工場の立地(山が近い、周辺に田畑があるなど)や、取り扱う食品の種類によって異なります。
一般的に、食品工場で問題となるのは以下のような害虫です。
- 飛行昆虫:コバエ類、ユスリカ、ハエなど
- 歩行昆虫:ゴキブリ類、アリ類など
- 貯穀害虫:シバンムシ、コクゾウムシなど(特に粉ものを扱う工場)
1-3. 管理基準(閾値)の設定
管理基準(閾値)とは、「捕獲数が何匹を超えたら、何らかの対策(是正措置)を講じる」というアクションのトリガーとなる基準値のことです。例えば、「Aエリアのライトトラップで1週間に5匹以上の飛翔昆虫が捕獲されたら、原因調査と清掃強化を行う」といった具体的なルールを定めます。この基準があることで、客観的な判断が可能になります。
ステップ2:トラップの選定と設置(Do)- 専門家が教える正しい置き方
計画ができたら、次はいよいよモニタリングツールであるトラップを設置します。トラップの性能を最大限に引き出すには、適切な種類を選び、適切な場所に設置することが不可欠です。
2-1. トラップの種類と特徴(ライトトラップ、歩行昆虫用トラップ等)
モニタリングに使用される主なトラップには、以下のものがあります。その特徴を以下の表にまとめましたので、選定の参考にしてください。
トラップの種類 | 主な対象 | 特徴 |
---|---|---|
ライトトラップ(捕虫器) | 飛翔昆虫(ハエ、ユスリカ等) | 光で虫を誘引し、粘着シートで捕獲する。広範囲の状況把握に適している。 |
歩行昆虫用トラップ | 歩行昆虫(ゴキブリ、アリ等) | 床や壁際に設置し、通りかかった虫を捕獲する。潜伏場所の特定に有効。 |
フェロモントラップ | 特定の貯穀害虫など | 性フェロモンで特定の種類の虫を強力に誘引する。対象種をピンポイントで調査したい場合に用いる。 |
2-2.【最重要】効果を最大化する設置場所と、やりがちなNG例
トラップは、ただ置けば良いというものではありません。監査官も「なぜ、ここに置いたのか」という設置根拠を見ています。効果的な設置場所と、よくある失敗例を理解しておきましょう。
<効果的な設置場所>
- 外部からの侵入経路:出入口、シャッターの下、壁の隙間など。
- 内部での発生源となりやすい場所:排水溝の周辺、原材料の保管場所、ゴミ置き場など。
- 製造ラインへの侵入リスクが高い場所:包装室の前など。
<やりがちなNG例>
- 製造ラインの真上:捕獲した虫が落下し、製品に混入するリスクがあります。
- 出入口の真正面(屋外向き):外部の虫を不要に誘引してしまいます。
- 水や蒸気がかかる場所:粘着シートが劣化し、捕獲性能が低下します。
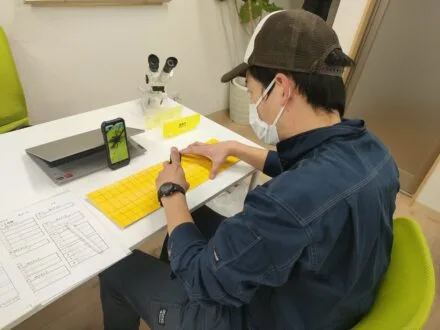
- 場所
- 大阪市・食品工場
- 施工場所
- 食品工場
モニタリングの結果、今まで気づかなかった害虫の侵入経路を特定することができました。早期に対策を講じたことで、大きな被害を防ぐことができ、本当に助かりました。専門家による定期的なモニタリングは、非常に効果的だと実感しています。…もっと読む
ステップ3:データの収集と記録(Check)- 証拠として通用する記録の付け方
設置したトラップの点検(チェック)を行い、結果を記録に残します。この「記録」こそが、HACCPが適切に運用されていることを示す客観的な証拠となります。「記録の付け方が分からない」というお悩みはよく伺いますが、ポイントを押さえれば難しくありません。
3-1. 頻度はどれくらいが適切か?
モニタリングの頻度は、工場のリスク評価に基づいて決定しますが、一般的には週に1回、または月に1回のペースで定期的に行うことが推奨されます。特に、虫の活動が活発になる夏場や、過去に問題が発生したエリアは、頻度を上げて重点的にチェックすると良いでしょう。
3-2.「いつ、どこで、誰が、何匹」を正確に記録する
監査で通用する記録にするためには、最低限、以下の項目を記録に残す必要があります。誰が見ても状況が分かるように、正確かつ客観的に記載することが重要です。
- 点検日:いつチェックしたか
- 点検場所:どのトラップか(トラップごとに番号を振っておくと良い)
- 点検者:誰がチェックしたか
- 捕獲数:何が何匹捕獲されたか(可能であれば虫の種類も同定する)
- 特記事項:トラップの破損、周辺の汚れなど、気づいた点を記載
- 是正措置:管理基準を超えた場合に、どのような対策を行ったかを記載
ステップ4:データ分析と評価(Analyze)- ただ数えるだけで終わらせない
記録したデータは、ただ保管しておくだけでは宝の持ち腐れです。データを分析し、工場内の衛生状態を評価して初めて、モニタリングは意味を持ちます。
4-1. グラフ化による傾向の「見える化」
数字の羅列だけでは、変化や異常を見つけるのは困難です。トラップごとの捕獲数を時系列の折れ線グラフにしたり、工場全体の捕獲数を月別の棒グラフにしたりすることで、傾向が「見える化」され、問題点を直感的に把握できます。
4-2. 季節変動や特定の原因との相関関係を探る
グラフを分析すると、「毎年、梅雨の時期にコバエが増える」「特定の原材料を搬入した週に、チャタテムシが増加する」といった、特定の事象との相関関係が見えてくることがあります。この「気づき」こそが、根本原因を特定し、効果的な対策を立案するための重要なヒントになります。
ステップ5:是正措置と改善(Action)- 問題発生時の対応と予防
モニタリングはPDCAサイクルの一部です。分析・評価の結果、問題が見つかれば、すぐに対応(是正措置)し、再発防止に繋げなければなりません。
5-1. 管理基準を超えた場合の具体的なアクションプラン
計画時に設定した管理基準(閾値)を超えた場合は、あらかじめ定めておいたアクションプランに従って、迅速に対応します。例えば、以下のような対応が考えられます。
- 発生源周辺の徹底的な清掃と殺菌
- 侵入経路となっている隙間や破損個所の特定と修繕
- 一時的な殺虫剤の使用(使用場所や薬剤は慎重に選定)
5-2. モニタリング計画自体の見直しと改善
是正措置の結果、捕獲数が管理基準内に収まったかを確認することも重要です。また、モニタリングを続ける中で、「この場所はほとんど捕獲されない」「このエリアはもっと重点的に監視すべきだ」といった改善点が見えてきます。定期的にモニタリング計画そのものを見直し、より効果的で効率的な体制へと改善していくことが求められます。
自社でやる?業者に頼む?メリット・デメリットと判断基準
ここまで具体的な手順を解説してきましたが、「これを全て自社でやるのは大変そうだ」と感じた方もいらっしゃるかもしれません。モニタリングは自社で行うことも、専門業者に委託することも可能です。それぞれのメリット・デメリットを理解し、自社に合った方法を選択しましょう。
自社対応(インハウス)のメリットと注意点
<メリット>
- 外部委託コストを削減できる。
- 担当者の知識やスキルが向上し、ノウハウが社内に蓄積される。
- 日々の変化に気づきやすく、迅速な対応が可能。
<注意点>
- 担当者の業務負担が大きく、通常業務を圧迫する可能性がある。
- 専門的な知識や虫の同定スキルが不足し、正確な評価が難しい場合がある。
- 判断が主観的になりやすく、問題を見過ごすリスクがある。
専門業者への委託のメリットと注意点
<メリット>
- 豊富な専門知識と経験に基づいた、質の高いモニタリングが期待できる。
- 第三者の客観的な視点で、自社では気づけないリスクを指摘してもらえる。
- 監査や査察の際に、専門家による客観的な報告書が強力な証拠となる。
- 従業員は本来の業務に集中できる。
<注意点>
- 外部委託のコストが発生する。
- 業者によって知識やサービスの質に差があるため、慎重な選定が必要。
- 業者に任せきりになり、社内の衛生意識が低下する可能性がある。
よくあるご質問(FAQ)
ここでは、食品工場の担当者様から、私たちによく寄せられるご質問とその回答をご紹介します。
Q1. モニタリングで特に注意すべき虫の種類は何ですか?
A1. 特に注意すべきは、コバエ類(ショウジョウバエ、ノミバエ)とゴキブリ類です。コバエ類は食品に直接産卵したり、食中毒菌を媒介したりするリスクがあり、ゴキブリ類は集団で繁殖しやすく、その存在自体が不衛生な印象を与えます。これらは多くの食品工場で共通の課題となるため、重点的な監視が必要です。
Q2. 捕虫器のランプはどれくらいの頻度で交換すべきですか?
A2. 一般的に、半年に1回、またはメーカーが推奨する交換時期に従って交換してください。捕虫器のランプは、目に見える光は出ていても、虫を誘引する特定の波長の紫外線は徐々に弱まっていきます。交換を怠ると、捕獲性能が著しく低下し、正しいモニタリングができなくなるため、定期的な交換が不可欠です。
Q3. 監査では記録のどこを一番見られますか?
A3. 監査官が最も重視するのは、「記録の継続性」と「管理基準を超えた際の是正措置の記録」です。記録が途切れることなく、定期的に実施されているか。そして、問題が起きた際に、それを放置せず、きちんと対応し、その内容が記録されているか。この2点が、HACCPが形骸化せず、有効に機能していることを示す重要な証拠と見なされます。
Q4. 食品工場での虫のモニタリングで害虫駆除会社に依頼する場合どのような点に注意して選べばいいですか?
A4. 業者選びで失敗しないためには、以下の点を確認することをおすすめします。
1. 食品工場の防虫実績が豊富か:一般家庭と食品工場では求められるレベルが全く異なります。
2. データに基づいた論理的な提案をしてくれるか:感覚ではなく、モニタリングデータに基づいた科学的なアプローチができる業者を選びましょう。
3. HACCPや食品安全規格への深い理解があるか:監査の視点を持ち、適切なアドバイスをくれるかが重要です。
私たち株式会社トータルクリーンでは、これらの条件を満たすことはもちろん、お客様の状況に合わせた最適なご提案をさせていただきます。
まとめ:虫モニタリングは、食品の安全と信頼を守る最前線です
今回は、食品工場における虫モニタリングの重要性から、具体的な実践方法、そして考え方までを網羅的に解説しました。
食品工場における虫モニタリングは、手間のかかる作業だと感じるかもしれません。しかし、これは製品の安全を守り、お客様からの信頼を維持し、ひいては企業のブランド価値を守るための、極めて重要な最前線の活動です。
この記事が、皆様の工場における衛生管理体制の強化の一助となれば幸いです。
もし、「自社だけでは難しそうだ」「一度、専門家の視点で見てほしい」といったお悩みがあれば、いつでも私たち株式会社トータルクリーンにご相談ください。食品工場における防虫対策の専門担当者が対応いたします。